The S-Press is a high precision, high pressure, steel frame roller-bearing swaging and reloading press. It has become the world's most popular home swaging press, replacing the prior Series II press, and the decades of Corbin's Silver Press and early Mity Mite presses.
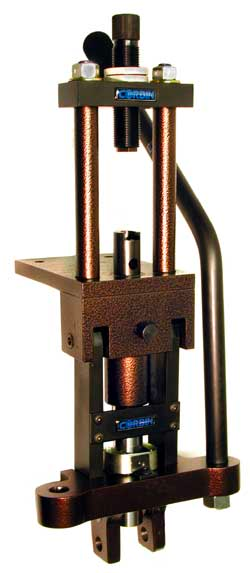
Here are some of the unique features of the S-Press, found in no other brand of swaging or reloading press...
- Head supported and kept in alignment by two torsion/compression pairs of struts.Corbin pioneered the aircraft-inspired torsion/compression strut, which consists of a heavy section of steel cylinder under high compression force, applied through a central rod under equal but opposite tension.
Hardened Grade 8 washers allow torque to be equally applied to each strut without shifting the critical alignment: a precision hardened alignment test jig is put into the press ram, and the press head is assembled with the test jig in place, making it impossible to assemble the press unless the head and ram are in exact axial alignment.
The compression/tension struts make the frame much more rigid than a single piece of metal or a cast frame. (Most cast frame presses advertise up to 40,000 psi tensile strength, whereas the frame of the CSP-1 exceeds 100,000 psi tensile strength). - Automatic ejection of bullets on the down stroke.The CSP-1 press has a tough stop pin that passes completely through the ram, and is supported on both sides by the frame. The hardened steel stop pin bears against the lower end (head) of the internal swage punch, stopping it as the ram and die are moved down, which in effect pushes the internal punch and the bullet out of the die when you lower the ram. This smooth, easy ejection of the bullet is quicker than using a separate ejector or a mallet, as you would do with a reloading press swage die. It is gentle, smooth, and uses the full power of the press leverage to eject the bullet without impact shock.
- Easily changed dual stroke leverage system for reloading and swaging.Instead of just getting the world's best selling swaging press with the longest history of improvements, you are also getting one of the world's most precise and accurately aligned benchrest grade reloading presses!
Benchrest shooters buy the CSP-1 for its great rigidity, precision alignment, and smooth roller-bearing operation...including shooters who do not swage bullets at all. The press changes from 2 inch swaging stroke to 4 inch reloading stroke in seconds, using a single hex key wrench to secure the hardened and ground pivot pin. - Removable head, so you can use any thread.The head of the CSP-1 press is a thick plate of steel, precision machined, bored, and threaded for either the standard 7/8-14 tpi, or for any custom thread you wish. Different heads can be provided for obsolete dies or those which may be developed in the future.
Corbin also makes "field alignment" jigs to go with the heads, precision machined ram-to-head alignment tools you can use to adjust any head plate to exact alignment with the ram. Without this, changing the heads would leave the press only slightly better aligned than competitive models. With it, you can quickly restore the "head and shoulders above" alignment that has kept the CSP-1 in such demand by knowledgable shooters and bullet research professionals.
|
The improvement never ends... ![]() ![]() ![]() ![]() A steel locking bar secures both the links to eliminate any side play and keep both of the ram link in perfect sync for smoother operation, reduced rotational torque on the ram, and longer life with higher alignment precision. It provides the aligment accuracy formerly achieved by benchrest loading dies used with arbor presses. ![]() The S-press frame is machined entirely of steel, with no castings, and has a tensile strength in excess of 100,000 psi (compared to the largest cast frame presses advertising 40,000 to 45,000 psi maximum). All links run in bearings, as does the ram (two inch-long oil-impregnated bronze bearings support and guide the ram inside its hydraulic cylinder sleeve housing). The press comes with a reloading adapter kit at no extra cost. It can be used in a 4-inch stroke configuration for reloading, or with a 2-inch stroke for swaging, simply by moving the ram pin to a different pair of holes in the linkage. A spent primer catcher tray comes with the press. The tray slips over the ram and rides up and down with the shell holder adapter (which takes standard RCBS button shell holders). Spent primers are rolled into the tray through an angled port in the shell holder/ram extension, as is all priming residue. The S-press (catalog number CSP-1) is a hand-made, assembled and tested product with an industrial hard-chromed ram (not the soft screw stock used in most mass produced, cast frame presses). The entire press frame and handle has an electro-coated metal and polyester powder coat finish baked not just on, but actually baked into the pores of the steel, so it will look good for years to come even after hard use. The finish resists corrosion, and looks great on your loading bench, without showing grease, lube, or residue stains. |
Press Head/Frame Dimensions for CSP-1, CSP-2 Models |
Alignment System:![]()
These errors were corrected in Corbin presses with the following procedures, which pointed out other, smaller corrections which were hidden until the alignment precision was brought into a much closer tolerance than is possible with conventional press construction. Then, these lesser factors were identified and corrected, one by one. Many are caused by errors so small that they only become apparent when the larger issues are solved, such as the slight angle between the threaded bore of commercial nuts to their bearing surfaces, or the variance in thickness of standard washers from one side to the other. Time consuming machine work is required on every piece of hardware if these sources of uneven stress are to be eliminated. Lower cost press manufacturers simply cannot afford to take all the extra time these many steps require (and, for less demanding work, it isn't required). |
The bottoms of each of the nuts is lathe turned for flatness using a jig that maintains exact right angle to the bore of the nut. (Commonly purchased nuts usually show considerable tilt or angular misalignment between the true axis of the nut's threads, and the bearing surface of the nut, which will push the threaded rod slightly to one side as you tighten the nut.) Assembly is done with the alignment jig in place, so it could not be removed if there was any misalignment in any direction. This assures the machinist he has done it correctly: he cannot go on if the press isn't exactly aligned so his alignment tool can slide out of the press. ![]() Next, a black-oxide finished steel top plate, bored on the same spacing as the base block, is slipped over the longer threaded torsion rods and rests on the top of the compression cylinders. The holes through which the rods pass are slightly larger than the rod diameter, to allow for adjustment of alignment. A precision alignment tool, which is similar to the press ram with a machined section on top that just passes through the 7/8-14 threaded hole in the top plate, is inserted in the press, and used to align the top plate. ![]() The torsion/compression support design keeps constant tension on the rod and cylinder, so that side torque has less bending movement than it would on a similar diameter of solid rod. The links are individually fitted with four sets of Torrington roller needle bearings running on hardened and ground pins. The bearings are covered by the toggle arms at one end and the press block at the other, so they are not apparent unless the press links are removed. Because many of features of the CSP-1 press are hidden, greater appreciation of the work that goes into building it comes from comparing its smooth operation, high strength and power, and extreme precision, with the typical over-the-counter retail presses. The net result of these detailed efforts is a tool orders of magnitude more accurate than those which must be built to sell through two or three levels of distribution markups to the end user. If the standard rule of thumb is that retail pricing is about 4 times cost of manufacture, to allow for profit for manufacturer, jobber, distributor, and dealer, it means a $100 press has about $25 worth of parts and labor in it at the factory door. Obviously, one can use better materials, design and construction when the end price does not contain distribution markups. |
Optional Accessories |
![]() Self-supporting heavy duty steel floor stand with mounting bolt holes for either the CSP-1 or CSP-2 press. Tough wood fiber deck puts your own weight into the system so you are the anchor; no holes in the floor, no braces required for solid reliable operation. (Truck shipment only, 150-lbs). One-inch thick top plate is tapped for both the S-Press and the Mega Mite press (click photo for hole pattern layout). Adjustable height for convenient, easier operation. Set to suit your needs! |
![]() |
![]() |
![]() |
![]() While we're at it, the primer tray (CSP-T) and the reloading adapter (CSP-R) come with the press as well, but are available as replacements or spares. The primer tray fits over the ram and rides up and down with it, catching spent primers and primer residue that roll out of the angled ejection port on the reloading adapter. The reloading adapter (CSP-A) is a combined button shell holder adapter and ram extension with a primer port on the side. It takes standard RCBS-type button shell holders, securing them with a ball bearing detent. |
![]() The long handle requires more "reach" than is necessary for most operations, so you will probably want to keep the standard handle. It doesn't require quite so much stretching as the long handle, but when you need it, the additional power is welcome! The CSP-1 comes standard with the CSP-1SH standard handle, but this handle is also available as a replacement item. Roller side-bar handles similar to those used on the CSP-2 Mega Mite can be provided on special order. |
![]() The CSP-1 comes standard with the CSP-1SH standard handle, but the roller handle is available as a replacement item. Roller side-bar handles (similar to those used on the CSP-2 Mega Mite) are not a standard "listed" item but can be special ordered. They are the same price as the CSP-2-SH which is the roller sidebar handle for the Mega-Mite, and in fact is the same except for the diameter of the threads attaching it to the press toggle. |
![]() ![]() Packaging information: Shipping weight 22 lbs. Carton size: Length = 19 in, Width = 11 in, Height = 9 in. |
![]() Mounting pattern for both CSP-1 and CSP-2 presses (left). The CSP-1 S-Press mounting holes are the three inside; the CSP-2 Mega Mite uses the three larger outside holes. CSP-1 Ram Dimensions CORBIN |
Start writing here...
About Corbin S-Press