PUNCH-H is a general punch type for the -H series of dies, which includes external punches, internal punches, and drawing punches (which fit directly in the press ram). External punches include the core swage external, and various end-shapes and diameters of core seating punches which fit either the ID of a jacket or the ID of the die. All external punches for swage dies fit into the floating punch holder, in the head of the press, and are retained by a bushing in the punch holder. Internal punches drop into the press ram, and do not come out of the die during operation. The length of the punch head determines how far the punch drops into the ram, and thus sets the position of the other end of the punch within the die. Longer and heavier bullets use shorter punch heads. Punches for drawing jackets or bullets fit into the press ram, and push the component through a draw die that fits the press head (instead of the usual punch holder).
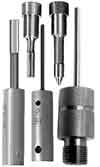
Punch Types | |
![]() | PUNCH-H is a general punch type for the -H series of dies, which includes external punches, internal punches, and drawing punches (which fit directly in the press ram). External punches include the core swage external, and various end-shapes and diameters of core seating punches which fit either the ID of a jacket or the ID of the die. All external punches for swage dies fit into the floating punch holder, in the head of the press, and are retained by a bushing in the punch holder. Internal punches drop into the press ram, and do not come out of the die during operation. The length of the punch head determines how far the punch drops into the ram, and thus sets the position of the other end of the punch within the die. Longer and heavier bullets use shorter punch heads. Punches for drawing jackets or bullets fit into the press ram, and push the component through a draw die that fits the press head (instead of the usual punch holder). |
![]() | PUNCH-HA Adjustable Length (core seating or tubing end rounding), for tubing or jackets under 0.5-inch OD. This -H type adjustable punch has a micrometer-like barrel which adjusts on screw threads relative to the central portion, moving the shoulder to the desired position for a given length of tubing or jacket. In rebated boattail core seating, soft or thin jacket materials may tend to extrude forward and lengthen the jacket, taking material from the base section. This may be so severe that the jacket separates. However, even if it is not, the adjustable shoulder can be set to prevent random lengthening of the jacket because of the force of the lead trying to push forward. Adjustable shouldered punches are economical when three or more different jacket lengths may be desired, as each length would otherwise require a separate fixed shoulder length punch. |
![]() | PUNCH-HL Adjustable Length (core seating or tubing end rounding), for Large diameter tubing, 1/2-inch OD and up. Similar to the PUNCH-HA in concept, the larger size components require a different internal construction. This -H type adjustable punch has a micrometer-like barrel which adjusts on screw threads relative to the central portion, moving the shoulder to the desired position for a given length of tubing or jacket. In rebated boattail core seating, soft or thin jacket materials may tend to extrude forward and lengthen the jacket, taking material from the base section. This may be so severe that the jacket separates. However, even if it is not, the adjustable shoulder can be set to prevent random lengthening of the jacket because of the force of the lead trying to push forward. Adjustable shouldered punches are economical when three or more different jacket lengths may be desired, as each length would otherwise require a separate fixed shoulder length punch. |
![]() | PUNCH-HA Adjustable Length internal punch can be made for any die, but generally is used with a point forming die (to seal the end of the cavity for use with lead tip or all-lead bullets). The purpose of the adjustable length section is to position the end of the punch or ejection pin exactly at the end of the bullet shaped cavity so the punch seals pressure at the tip of the cavity. This prevents lead from extruding up the ejection pin hole, and allows higher pressure to be used for extrusion in custom weight-adjusting point form dies. |
![]() | PUNCH-HF Extra long funnel punch, for use with powdered metals and the Corbin FUNNEL-H precision funnel, helps you seat the powdered material into a jacket. Powder is loosely packed by its own weight, and takes up considerably more space before being compressed by seating. In fact, it takes up so much room that it won't all fit into the jacket in most cases. A normal core seating punch would simply push through the powder, blowing powder past it until it finally reached the jacket. A full die bore diameter seating punch would compress the powder to the edge of the jacket but couldn't enter the jacket. The funnel is made with a precision spout, which exactly matches the jacket wall thickness. The spouts are replaceable, and the funnel body is universal for all jackets and calibers. An extra long core seating punch pushes the column of powder through the funnel and down into the jacket without loss. |
![]() | PUNCH-HX is a special kind of custom -H punch (could be specified as a PUNCH-HC, external, core seat or core swage, X-style or cruciform) made either to fit a core swage, or a core seat die, and to put a deep X-cut into the lead core. When used with a core swage die, the x-cut core is coated or filled with lubricant or a powdered filler to prevent the cuts from closing entirely in the core seating operation. When used with a core seating die, the core is normally seated first with a regular flat end or hollow point core seat punch, and then the X is pressed into the core. The purpose is to help the bullet expand evenly into four "petals" as the jacket ruptures and expands on impact. |
Punch Types | |
![]() | PUNCH-H is a general punch type for the -H series of dies, which includes external punches, internal punches, and drawing punches (which fit directly in the press ram). External punches include the core swage external, and various end-shapes and diameters of core seating punches which fit either the ID of a jacket or the ID of the die. All external punches for swage dies fit into the floating punch holder, in the head of the press, and are retained by a bushing in the punch holder. Internal punches drop into the press ram, and do not come out of the die during operation. The length of the punch head determines how far the punch drops into the ram, and thus sets the position of the other end of the punch within the die. Longer and heavier bullets use shorter punch heads. Punches for drawing jackets or bullets fit into the press ram, and push the component through a draw die that fits the press head (instead of the usual punch holder). |
![]() | PUNCH-HA Adjustable Length (core seating or tubing end rounding), for tubing or jackets under 0.5-inch OD. This -H type adjustable punch has a micrometer-like barrel which adjusts on screw threads relative to the central portion, moving the shoulder to the desired position for a given length of tubing or jacket. In rebated boattail core seating, soft or thin jacket materials may tend to extrude forward and lengthen the jacket, taking material from the base section. This may be so severe that the jacket separates. However, even if it is not, the adjustable shoulder can be set to prevent random lengthening of the jacket because of the force of the lead trying to push forward. Adjustable shouldered punches are economical when three or more different jacket lengths may be desired, as each length would otherwise require a separate fixed shoulder length punch. |
![]() | PUNCH-HL Adjustable Length (core seating or tubing end rounding), for Large diameter tubing, 1/2-inch OD and up. Similar to the PUNCH-HA in concept, the larger size components require a different internal construction. This -H type adjustable punch has a micrometer-like barrel which adjusts on screw threads relative to the central portion, moving the shoulder to the desired position for a given length of tubing or jacket. In rebated boattail core seating, soft or thin jacket materials may tend to extrude forward and lengthen the jacket, taking material from the base section. This may be so severe that the jacket separates. However, even if it is not, the adjustable shoulder can be set to prevent random lengthening of the jacket because of the force of the lead trying to push forward. Adjustable shouldered punches are economical when three or more different jacket lengths may be desired, as each length would otherwise require a separate fixed shoulder length punch. |
![]() | PUNCH-HA Adjustable Length internal punch can be made for any die, but generally is used with a point forming die (to seal the end of the cavity for use with lead tip or all-lead bullets). The purpose of the adjustable length section is to position the end of the punch or ejection pin exactly at the end of the bullet shaped cavity so the punch seals pressure at the tip of the cavity. This prevents lead from extruding up the ejection pin hole, and allows higher pressure to be used for extrusion in custom weight-adjusting point form dies. |
![]() | PUNCH-HF Extra long funnel punch, for use with powdered metals and the Corbin FUNNEL-H precision funnel, helps you seat the powdered material into a jacket. Powder is loosely packed by its own weight, and takes up considerably more space before being compressed by seating. In fact, it takes up so much room that it won't all fit into the jacket in most cases. A normal core seating punch would simply push through the powder, blowing powder past it until it finally reached the jacket. A full die bore diameter seating punch would compress the powder to the edge of the jacket but couldn't enter the jacket. The funnel is made with a precision spout, which exactly matches the jacket wall thickness. The spouts are replaceable, and the funnel body is universal for all jackets and calibers. An extra long core seating punch pushes the column of powder through the funnel and down into the jacket without loss. |
![]() | PUNCH-HX is a special kind of custom -H punch (could be specified as a PUNCH-HC, external, core seat or core swage, X-style or cruciform) made either to fit a core swage, or a core seat die, and to put a deep X-cut into the lead core. When used with a core swage die, the x-cut core is coated or filled with lubricant or a powdered filler to prevent the cuts from closing entirely in the core seating operation. When used with a core seating die, the core is normally seated first with a regular flat end or hollow point core seat punch, and then the X is pressed into the core. The purpose is to help the bullet expand evenly into four "petals" as the jacket ruptures and expands on impact. |
![]() | PUNCH-HS is a special kind of custom -H punch (could be specified as a PUNCH-HC, internal, core seat, Saber Tooth or cruciform) made to fit a core seat die, and to put a a series of six notched in the jacket end. The Saber Tooth design is used only after the lead core has been seated conventionally. The seated core and jacket is then reversed, with the internal punch being changed to the Saber Tooth, and pushed open end first into the die. Sufficient lead must be left to cushion and support the teeth, and the punch must be a very close fit to the die bore, to prevent breaking the sharp, thin teeth. The resulting bullet tends to open more quickly and evenly. |
![]() | PUNCH-S is a general punch type for the -S series of dies, which includes external punches, internal punches, and drawing punches (which fit directly in the press ram). External punches include the core swage external, and various end-shapes and diameters of core seating punches which fit either the ID of a jacket or the ID of the die. All external punches for swage dies fit into the floating punch holder, in the head of the press, and are retained by a bushing in the punch holder. Internal punches drop into the press ram, and do not come out of the die during operation. The length of the punch head determines how far the punch drops into the ram, and thus sets the position of the other end of the punch within the die. Longer and heavier bullets use shorter punch heads. Punches for drawing jackets or bullets fit into the press ram, and push the component through a draw die that fits the press head (instead of the usual punch holder). |
![]() | PUNCH-SA Adjustable Length (core seating or tubing end rounding), for tubing or jackets under 0.5-inch OD. This -S type adjustable punch has a micrometer-like barrel which adjusts on screw threads relative to the central portion, moving the shoulder to the desired position for a given length of tubing or jacket. In rebated boattail core seating, soft or thin jacket materials may tend to extrude forward and lengthen the jacket, taking material from the base section. This may be so severe that the jacket separates. However, even if it is not, the adjustable shoulder can be set to prevent random lengthening of the jacket because of the force of the lead trying to push forward. Adjustable shouldered punches are economical when three or more different jacket lengths may be desired, as each length would otherwise require a separate fixed shoulder length punch. |
![]() | PUNCH-SL Adjustable Length (core seating or tubing end rounding), for Large diameter tubing, 1/2-inch OD. Similar to the PUNCH-SA in concept, the larger size components require a different internal construction. This -S type adjustable punch has a micrometer-like barrel which adjusts on screw threads relative to the central portion, moving the shoulder to the desired position for a given length of tubing or jacket. In rebated boattail core seating, soft or thin jacket materials may tend to extrude forward and lengthen the jacket, taking material from the base section. This may be so severe that the jacket separates. However, even if it is not, the adjustable shoulder can be set to prevent random lengthening of the jacket because of the force of the lead trying to push forward. Adjustable shouldered punches are economical when three or more different jacket lengths may be desired, as each length would otherwise require a separate fixed shoulder length punch. |
![]() | PUNCH-SA Adjustable Length internal punch can be made for any die, but generally is used with a point forming die (to seal the end of the cavity for use with lead tip or all-lead bullets). The purpose of the adjustable length section is to position the end of the punch or ejection pin exactly at the end of the bullet shaped cavity so the punch seals pressure at the tip of the cavity. This prevents lead from extruding up the ejection pin hole, and allows higher pressure to be used for extrusion in custom weight-adjusting point form dies. |
![]() | PUNCH-SF Extra long funnel punch, for use with powdered metals and the Corbin FUNNEL-S precision funnel, helps you seat the powdered material into a jacket. Powder is loosely packed by its own weight, and takes up considerably more space before being compressed by seating. In fact, it takes up so much room that it won't all fit into the jacket in most cases. A normal core seating punch would simply push through the powder, blowing powder past it until it finally reached the jacket. A full die bore diameter seating punch would compress the powder to the edge of the jacket but couldn't enter the jacket. The funnel is made with a precision spout, which exactly matches the jacket wall thickness. The spouts are replaceable, and the funnel body is universal for all jackets and calibers. An extra long core seating punch pushes the column of powder through the funnel and down into the jacket without loss. |
![]() | PUNCH-SX is a special kind of custom -S punch (could be specified as a PUNCH-HC, external, core seat or core swage, X-style or cruciform) made either to fit a core swage, or a core seat die, and to put a deep X-cut into the lead core. When used with a core swage die, the x-cut core is coated or filled with lubricant or a powdered filler to prevent the cuts from closing entirely in the core seating operation. When used with a core seating die, the core is normally seated first with a regular flat end or hollow point core seat punch, and then the X is pressed into the core. The purpose is to help the bullet expand evenly into four "petals" as the jacket ruptures and expands on impact. |
![]() | PUNCH-SS is a special kind of custom -S punch (could be specified as a PUNCH-SC, internal, core seat, Saber Tooth or cruciform) made to fit a core seat die, and to put a a series of six notched in the jacket end. The Saber Tooth design is used only after the lead core has been seated conventionally. The seated core and jacket is then reversed, with the internal punch being changed to the Saber Tooth, and pushed open end first into the die. Sufficient lead must be left to cushion and support the teeth, and the punch must be a very close fit to the die bore, to prevent breaking the sharp, thin teeth. The resulting bullet tends to open more quickly and evenly. |
![]() | PUNCH-S Internal Core Seat, Flat Base (Int CS-FB) is the general description of the punch that stays inside the core seating die and ejects the components on the down stroke of the press. The internal core seater can also have a cup base shape (slight dome), dish base (slight curve), hollow base (conical projection), or Base Guard(TM) base (small depression in center). The internal core seater punch looks very much like the internal core swage punch, but is larger in diameter. The punch end opposite the working face is called the "head". Oddly enough, the head also has a "tail" which is the reduced portion at the very end. The length of this reduced portion determines the position of the punch face within the die at the top of the swaging stroke, which in turn controls how long or heavy a bullet will fit into the die. Shorter heads (longer tails) mean heavier bullets can be made. Very light bullets may require a longer head (shorter tail) to hold the punch closer to the die mouth. |
![]() | PUNCH-S Internal Point Form is also called the "ejection" punch (Int.PF). It consists of a long single diameter punch head with a hardened spring steel ejection pin secured to one end. A hole runs through the head of the punch. The stop pin that is located in the front of the CSP-1 press goes through this hole, and secures the punch to the frame of the press. With the punch fastened to the press frame, the die moves up with the ram and the punch is retracted from the die cavity. This keeps the punch from being trapped in the end of the bullet jacket when the ogive is formed. Earlier punches for the -M type die used a slot instead of a hole, and a shorter stop pin. Both kinds can be used in the current -S presses. Ejection pin wires are available for replacement in packages of 5 wires. Diameter depends on caliber and ogive, but is marked on the mouth of the swage die. |
Punch Types | |
![]() | PUNCH-H is a general punch type for the -H series of dies, which includes external punches, internal punches, and drawing punches (which fit directly in the press ram). External punches include the core swage external, and various end-shapes and diameters of core seating punches which fit either the ID of a jacket or the ID of the die. All external punches for swage dies fit into the floating punch holder, in the head of the press, and are retained by a bushing in the punch holder. Internal punches drop into the press ram, and do not come out of the die during operation. The length of the punch head determines how far the punch drops into the ram, and thus sets the position of the other end of the punch within the die. Longer and heavier bullets use shorter punch heads. Punches for drawing jackets or bullets fit into the press ram, and push the component through a draw die that fits the press head (instead of the usual punch holder). |
![]() | PUNCH-HA Adjustable Length (core seating or tubing end rounding), for tubing or jackets under 0.5-inch OD. This -H type adjustable punch has a micrometer-like barrel which adjusts on screw threads relative to the central portion, moving the shoulder to the desired position for a given length of tubing or jacket. In rebated boattail core seating, soft or thin jacket materials may tend to extrude forward and lengthen the jacket, taking material from the base section. This may be so severe that the jacket separates. However, even if it is not, the adjustable shoulder can be set to prevent random lengthening of the jacket because of the force of the lead trying to push forward. Adjustable shouldered punches are economical when three or more different jacket lengths may be desired, as each length would otherwise require a separate fixed shoulder length punch. |
![]() | PUNCH-HL Adjustable Length (core seating or tubing end rounding), for Large diameter tubing, 1/2-inch OD and up. Similar to the PUNCH-HA in concept, the larger size components require a different internal construction. This -H type adjustable punch has a micrometer-like barrel which adjusts on screw threads relative to the central portion, moving the shoulder to the desired position for a given length of tubing or jacket. In rebated boattail core seating, soft or thin jacket materials may tend to extrude forward and lengthen the jacket, taking material from the base section. This may be so severe that the jacket separates. However, even if it is not, the adjustable shoulder can be set to prevent random lengthening of the jacket because of the force of the lead trying to push forward. Adjustable shouldered punches are economical when three or more different jacket lengths may be desired, as each length would otherwise require a separate fixed shoulder length punch. |
![]() | PUNCH-HA Adjustable Length internal punch can be made for any die, but generally is used with a point forming die (to seal the end of the cavity for use with lead tip or all-lead bullets). The purpose of the adjustable length section is to position the end of the punch or ejection pin exactly at the end of the bullet shaped cavity so the punch seals pressure at the tip of the cavity. This prevents lead from extruding up the ejection pin hole, and allows higher pressure to be used for extrusion in custom weight-adjusting point form dies. |
![]() | PUNCH-HF Extra long funnel punch, for use with powdered metals and the Corbin FUNNEL-H precision funnel, helps you seat the powdered material into a jacket. Powder is loosely packed by its own weight, and takes up considerably more space before being compressed by seating. In fact, it takes up so much room that it won't all fit into the jacket in most cases. A normal core seating punch would simply push through the powder, blowing powder past it until it finally reached the jacket. A full die bore diameter seating punch would compress the powder to the edge of the jacket but couldn't enter the jacket. The funnel is made with a precision spout, which exactly matches the jacket wall thickness. The spouts are replaceable, and the funnel body is universal for all jackets and calibers. An extra long core seating punch pushes the column of powder through the funnel and down into the jacket without loss. |
![]() | PUNCH-HX is a special kind of custom -H punch (could be specified as a PUNCH-HC, external, core seat or core swage, X-style or cruciform) made either to fit a core swage, or a core seat die, and to put a deep X-cut into the lead core. When used with a core swage die, the x-cut core is coated or filled with lubricant or a powdered filler to prevent the cuts from closing entirely in the core seating operation. When used with a core seating die, the core is normally seated first with a regular flat end or hollow point core seat punch, and then the X is pressed into the core. The purpose is to help the bullet expand evenly into four "petals" as the jacket ruptures and expands on impact. |
![]() | PUNCH-HS is a special kind of custom -H punch (could be specified as a PUNCH-HC, internal, core seat, Saber Tooth or cruciform) made to fit a core seat die, and to put a a series of six notched in the jacket end. The Saber Tooth design is used only after the lead core has been seated conventionally. The seated core and jacket is then reversed, with the internal punch being changed to the Saber Tooth, and pushed open end first into the die. Sufficient lead must be left to cushion and support the teeth, and the punch must be a very close fit to the die bore, to prevent breaking the sharp, thin teeth. The resulting bullet tends to open more quickly and evenly. |
![]() | PUNCH-S is a general punch type for the -S series of dies, which includes external punches, internal punches, and drawing punches (which fit directly in the press ram). External punches include the core swage external, and various end-shapes and diameters of core seating punches which fit either the ID of a jacket or the ID of the die. All external punches for swage dies fit into the floating punch holder, in the head of the press, and are retained by a bushing in the punch holder. Internal punches drop into the press ram, and do not come out of the die during operation. The length of the punch head determines how far the punch drops into the ram, and thus sets the position of the other end of the punch within the die. Longer and heavier bullets use shorter punch heads. Punches for drawing jackets or bullets fit into the press ram, and push the component through a draw die that fits the press head (instead of the usual punch holder). |
![]() | PUNCH-SA Adjustable Length (core seating or tubing end rounding), for tubing or jackets under 0.5-inch OD. This -S type adjustable punch has a micrometer-like barrel which adjusts on screw threads relative to the central portion, moving the shoulder to the desired position for a given length of tubing or jacket. In rebated boattail core seating, soft or thin jacket materials may tend to extrude forward and lengthen the jacket, taking material from the base section. This may be so severe that the jacket separates. However, even if it is not, the adjustable shoulder can be set to prevent random lengthening of the jacket because of the force of the lead trying to push forward. Adjustable shouldered punches are economical when three or more different jacket lengths may be desired, as each length would otherwise require a separate fixed shoulder length punch. |
![]() | PUNCH-SL Adjustable Length (core seating or tubing end rounding), for Large diameter tubing, 1/2-inch OD. Similar to the PUNCH-SA in concept, the larger size components require a different internal construction. This -S type adjustable punch has a micrometer-like barrel which adjusts on screw threads relative to the central portion, moving the shoulder to the desired position for a given length of tubing or jacket. In rebated boattail core seating, soft or thin jacket materials may tend to extrude forward and lengthen the jacket, taking material from the base section. This may be so severe that the jacket separates. However, even if it is not, the adjustable shoulder can be set to prevent random lengthening of the jacket because of the force of the lead trying to push forward. Adjustable shouldered punches are economical when three or more different jacket lengths may be desired, as each length would otherwise require a separate fixed shoulder length punch. |
![]() | PUNCH-SA Adjustable Length internal punch can be made for any die, but generally is used with a point forming die (to seal the end of the cavity for use with lead tip or all-lead bullets). The purpose of the adjustable length section is to position the end of the punch or ejection pin exactly at the end of the bullet shaped cavity so the punch seals pressure at the tip of the cavity. This prevents lead from extruding up the ejection pin hole, and allows higher pressure to be used for extrusion in custom weight-adjusting point form dies. |
![]() | PUNCH-SF Extra long funnel punch, for use with powdered metals and the Corbin FUNNEL-S precision funnel, helps you seat the powdered material into a jacket. Powder is loosely packed by its own weight, and takes up considerably more space before being compressed by seating. In fact, it takes up so much room that it won't all fit into the jacket in most cases. A normal core seating punch would simply push through the powder, blowing powder past it until it finally reached the jacket. A full die bore diameter seating punch would compress the powder to the edge of the jacket but couldn't enter the jacket. The funnel is made with a precision spout, which exactly matches the jacket wall thickness. The spouts are replaceable, and the funnel body is universal for all jackets and calibers. An extra long core seating punch pushes the column of powder through the funnel and down into the jacket without loss. |
![]() | PUNCH-SX is a special kind of custom -S punch (could be specified as a PUNCH-HC, external, core seat or core swage, X-style or cruciform) made either to fit a core swage, or a core seat die, and to put a deep X-cut into the lead core. When used with a core swage die, the x-cut core is coated or filled with lubricant or a powdered filler to prevent the cuts from closing entirely in the core seating operation. When used with a core seating die, the core is normally seated first with a regular flat end or hollow point core seat punch, and then the X is pressed into the core. The purpose is to help the bullet expand evenly into four "petals" as the jacket ruptures and expands on impact. |
![]() | PUNCH-SS is a special kind of custom -S punch (could be specified as a PUNCH-SC, internal, core seat, Saber Tooth or cruciform) made to fit a core seat die, and to put a a series of six notched in the jacket end. The Saber Tooth design is used only after the lead core has been seated conventionally. The seated core and jacket is then reversed, with the internal punch being changed to the Saber Tooth, and pushed open end first into the die. Sufficient lead must be left to cushion and support the teeth, and the punch must be a very close fit to the die bore, to prevent breaking the sharp, thin teeth. The resulting bullet tends to open more quickly and evenly. |
![]() | PUNCH-S Internal Core Seat, Flat Base (Int CS-FB) is the general description of the punch that stays inside the core seating die and ejects the components on the down stroke of the press. The internal core seater can also have a cup base shape (slight dome), dish base (slight curve), hollow base (conical projection), or Base Guard(TM) base (small depression in center). The internal core seater punch looks very much like the internal core swage punch, but is larger in diameter. The punch end opposite the working face is called the "head". Oddly enough, the head also has a "tail" which is the reduced portion at the very end. The length of this reduced portion determines the position of the punch face within the die at the top of the swaging stroke, which in turn controls how long or heavy a bullet will fit into the die. Shorter heads (longer tails) mean heavier bullets can be made. Very light bullets may require a longer head (shorter tail) to hold the punch closer to the die mouth. |
![]() | PUNCH-S Internal Point Form is also called the "ejection" punch (Int.PF). It consists of a long single diameter punch head with a hardened spring steel ejection pin secured to one end. A hole runs through the head of the punch. The stop pin that is located in the front of the CSP-1 press goes through this hole, and secures the punch to the frame of the press. With the punch fastened to the press frame, the die moves up with the ram and the punch is retracted from the die cavity. This keeps the punch from being trapped in the end of the bullet jacket when the ogive is formed. Earlier punches for the -M type die used a slot instead of a hole, and a shorter stop pin. Both kinds can be used in the current -S presses. Ejection pin wires are available for replacement in packages of 5 wires. Diameter depends on caliber and ogive, but is marked on the mouth of the swage die. |
![]() | PUNCH-R is a general catalog number for standard punches that fit reloading press dies, including draw dies for jackets and bullets, Pro-Swage dies, and other -R type swage dies. External punches have a button-type head that slips into the slotted press ram, like a shell holder. Internal punches have a cylindrical head that keeps them from dropping out of the die. Swage dies for reloading presses screw into the 7/8-14 threaded head of the press, as do draw dies. The -R dies are further described by their caliber or diameter, the die into which they fit, and any specific shape such as "HP" for hollow point, or "CB" for cup base. (See terminology page for details.) |
Core Seating Punch Fit to Jacket ID When seating a lead core into a bullet jacket, there are two basic fits for the external seating punch:
With a core seated longer than the jacket, the punch fits the die bore snugly, and the jacket and core expand together, so long as the punch is a good fit in the die. Lead tip core seating punches are independent of the jacket wall thickness or ID, since they only need to fit the die itself. Sometimes the lead core tends to flow between the end of the jacket and the die wall, and leaves a small amount of lead film over the end of the jacket while the rest of the jacket exands correctly. If this should happen, the solution is to use a round nosed punch to expand or bell the mouth of the jacket, so it creates a pressure seal against the die wall. In most cases, the jackets expand quickly enough so that this isn't needed. But it is good to know that the technique can be used for stubborn jackets that require more expansion pressure than usual near the mouth. Open Tip Core Seating (or smaller exposed lead tips) ![]() You would think that the core seating punch would be a firm hand fit into the jacket. This would be reasonable if jackets didn't expand from core seating by as much as 0.002 inches. However, they do. So you must use a core seating punch that is larger than the initial ID of the jacket, in order to maintain a high pressure seal as the jacket expands. This means that the correct size of core seating punch is probably NOT going to be an easy fit into the jacket! In fact, it may be impossible to insert the punch by hand. The edge of the punch probably will have a small radius so it can be force-fitted into the jacket using the press leverage. The jacket will expand, from the compressed lead pressure, until it contacts the die wall and stops. The "sticking jacket" problem: But this creates a problem: the jacket is only expanded where lead has expanded it. The part of the jacket with the punch inserted into it does not expand beyond whatever the punch itself causes when it is forced in. That means the jacket is tightly held on the punch. When the ram is lowered, the jacket may "stick" on the punch and be pulled out of the die, instead of staying in the die so it can be properly ejected. To solve this problem, use little or no lubricant on the OD of the jacket. Wipe a little lube on the punch before inserting it into the jacket. Hold the pressure for a second or so, to allow the lead to expand the jacket fully. The only thing that pulls the jacket off the seating punch is friction between the die wall and the jacket OD. If too little pressure is used, so that the jacket doesn't fully expand, there is little or no friction created. Not only is the jacket undersized but there is no force to extract the jacket from the seating punch. Beginning bullet makers often believe that the seating punch is "too big", when in reality it is the right size but the jacket simply has not yet been expanded enough. Using a little more pressure, holding it a second or so longer, using less or no lubricant on the jacket OD (but ONLY for core seating, never for point forming!), and wiping a film of lube on the seating punch all combine to cause the jacket to pull off the punch and then be ejected from the die on the down stroke of the ram. The diameter of the core seating punch may be correct for one jacket wall thickness, but not for a different jacket with a thicker or a thinner wall. The rule of thumb is to use a micrometer to measure the jacket before anything is done to it. Subtract this measurement from the caliber. Usually the core seating die is at least 0.0001 smaller than the caliber, so subtract another 0.0001 inches. Now you have the total amount of expansion which the jacket should accomplish when the core is seated. If you use a pin gauge, an inside micrometer, or a comparision procedure to determine the ID of the jacket, you have the starting size before the core is seated and the jacket expands. Most beginners think this is the diameter required for a core seating punch, but in fact the punch has to be larger by the amount of anticipated expansion which was just calculated. For example, let's assume the following...
Now, a core seating punch of 0.2750 inches would just fit into the jacket, but it wouldn't seal pressure when the jacket expands. The core seating die would be .308 - 0.0001 inches or 0.3079 diameter inside. The .3060 jacket OD will expand until it touches the die walls, and becomes 0.3079 under pressure. That is an expansion of .3079 - .3060 = 0.0019 inches. ![]() So the correct punch would be a very tight intereference fit into the jacket, and would need to be inserted using the press rather than by hand. This seems counter-intuitive to beginners, as they forget about the need to expand the jacket, and that the jacket will expand the same on the inside diameter as it does on the outside diameter. In our example, a punch of 0.2769 to 0.2770 would create an excellent pressure seal. Even if that size punch sticks in the jacket, using the right timing, pressure, and lubrication combination should allow the jacket to be pulled off the punch when the ram is retracted, taking the die and the jacket/core combination with it due to the firm grip between jacket OD and die ID. |
Different Seating Punch Diameters for Different Wall Thicknesses
Since the core seating punch diameter for open tip bullet core seating has to fit snugly, after seating the core, at the particular ID where the core comes to rest, it follows that if you are using a tapered wall bullet jacket, the ID will become smaller toward the jacket base.
Also, if you change brands or kinds of jackets, the wall thickness may not be the same as the jacket which was originally intended to be used with the core seat punch provided. For example, if you originally ordered the die set along with some Corbin J-30-125 jackets, and somewhere along the way decided to purchase a different brand of jacket, you may need a different diameter of core seating punch. If you radically change the wall thickness with the same die set, you may even need a different core swage die (CSW)! This can happen if you order a die set to use with a commercial drawn jacket with 0.024-inch thick walls and then decide later to add a copper tubing jacket making set, which will usually produce jackets with 0.035-inch thick walls.
Bear in mind that nearly all commercial drawn jackets will have a thick base which is drawn up into the walls when the jacket is produced, with the walls being drawn thinner as the jacket is further reduced and made longer. So a typical jacket might have walls that are 0.026 inches thick near the base, and 0.022 inches thick in the midpoint, with perhaps 0.018 inch thickness at the mouth.
This is just an arbitrary illustration. Actual jacket wall taper and thickness can be just about anything that the jacket maker wants to produce. But it points to another concern for the bullet maker. The weight of the bullet, for any given jacket, depends on the amount of lead core put into it. And the volume or weight of the core will vary the length of the core. You can make a 150 grain .308 bullet in the same jacket as a 180 grain bullet, by using a shorter core in the same length jacket. But the core will be seated much further down, closer to the base, and the jacket walls will likely be thicker there.
So, the same punch that works fine with a 180 or 190 grain bullet may actually be too large to work properly with a 150 to 165 grain bullet, assuming the same jacket with a different length of core is used.
A good way to determine the ID of a jacket is to use a set of pin gauges. These are available in sets, such as a set that goes from .100 to .250 inches in increments of 0.001, 0.005, or 0.010 inches. Usually the cost is based on the accuracy or tolerance of the pin diameters, and the number of pins in a given set. If you make large spread of calibers, a set of pins that covers a larger range of diameters would be useful.
In most cases, you would want the pins in increments of 0.001, but don't really need calibration lab precision. A standard shop grade set would be fine, in most cases. The purpose is to get reasonably close for a seating punch diameter, but there is some allowable range where the same diameter still works reasonably well, even if there is a narrow range where a given punch is "perfect" for a given weight.
The pin which fits to the bottom of the jacket tells you the largest size of swaged core (lead) that will fit and not trap air. If you use a larger core, which slides half way into the jacket and stops, then of course it acts like a piston and seals high pressure air under it. A way to solve this, other than using a smaller core, is to swage the core using a punch that makes a reduced "nose" or "rebated boat tail" on one end, and the insert this smaller end first into the jacket. This is an inexpensive way to convert an existing core swage die so it works well with a somewhat "too snug" jacket ID. All you need is one additional punch, to replace one of the standard flat end core swage punches.
The pin which fits at the distance into the jacket where your core will be seated (which is further in than just the loose core) tells you what diameter to start your calculation for seating punch size. You would add the amount of jacket expansion to this measurement, and that is the diameter of punch that will maintain a good pressure seal.
The expansion of the jacket is the caliber less about 0.0001 inches, minus the pin size that you just discovered. The 0.0001 inches is an approximate difference between final caliber and the size used to make the core seating die (or the rebated boattail dies, which replace the core seater for RBT bullets). If you discover that your core seating die, or rebated boattail dies, have a different size allowance, use it instead of the normal 0.0001 inches. This is not written in stone, but is just a general approximation.
Using the wrong core seating punch diameter generally results in undersized bullets. If you use too large of a punch, it impacts the jacket walls and digs into them, crushing the portion toward the base, and may be stopped before it can apply enough force to the lead core to fully expand the jacket. Wrinkles in the lower portion of the jacket, or a shortened jacket, may be symptoms as well.
Using too small a core seating punch lets the lead core spurt around the punch, which also reduces pressure and may fail to expand the jacket properly. So we have a situation where over a fairly narrow range, a given diameter of punch produces good expansion, and either a larger or a smaller punch makes the bullet come out smaller than it should. Often the results are not noticed until the bullet is processed through the point forming die.Then the effect of the incorrect size core seating punch is "blamed" on the point form die. "My point form die was made too small!" is sometimes heard, when all it takes to find out is to swage a lead core in the die, without a jacket, and measure it. Lead is a good "gauge" because it is "dead" material. It does not spring back like a jacket (except for hard lead, which we discourage anyway in swaging). Swaging a lead slug in your core seater, and another in your point former, then carefully measuring both with the same micrometer should give you a good comparison of their bore sizes.
There are three things you can do if you find the core seating punch does not work properly with your particular bullet:
- Use a longer or shorter core. This can point out issues with sticking or undersized bullets.
- Use a different jacket with proper wall thickness at the core weight desired.
- Order a different diameter core seating punch. To do this, send a sample lead core and jacket.
If you wish to order a different diameter core seating punch, it is helpful if you make a lead core exactly the same weight and length as the one you plan to use, and send a sample of the same jacket you plan to use with it. Then, we can be sure to test the punch with your materials, prepared by you, so we can discover whether there is anything unusual going on with the materials themselves.
You'd be amazed at the things that are discovered when no assumptions are made, and everything is tested as if it had not been seen before! Assuming that the jackets we have are identical to the ones we sold you last week is usually reasonable. Assuming your lead wire really is pure 99.95% lead is usually safe, especially if you just bought it from us.
But usually doesn't mean always. Maybe something unusual happened, a run of parts that was slightly different tolerance, a different heat treatment, some kind of contamination in transit, or that one in a million anomoly no one would imagine could happen because it never did, before this!
Long-time bullet makers have been absolutely positive that they were using the same jackets and lead we provided, and it turned out they'd picked up something else that happened to be right next to the correct ones. Or they were positive that they were using the right core seating die, and on inspection it turned out to be a lead tip forming die with the core seat punch inserted.
There have been just enough such mistakes so that even if we "know for sure", we still try to confirm by tests and measurements. It doesn't hurt to check once more, especially with situations where all the standard tests a customer can do at home don't provide the answer!
2004: Corbin Redesigns -S External Punch
The External Punch for Corbin type -M dies (fits S-press or the discontinued Silver Press) and type -S dies (fits S-press) has been redesigned to eliminate the separate spacer ring. The new punches have a head length that is twice as long as the original, which takes exactly the same space as the original punch head and spacer ring. The new punches therefore interchange with the old ones. The only difference is that the spacer ring (or ring bushing as it was also called) is no longer needed for the new punches. You can use either the old style, with ring, or the new style, without ring, in the same dies and with the same punch holder. Both work equally well.
Background:
An "external" punch is one which fits into a floating punch holder in the press head. An "internal" punch fits inside the die and press ram, and is used to eject the bullet on the down stroke of the press. External punches push the bullet components into the die mouth.
The original type -M and type -S die sets all used external punches that were held in the punch holder by a threaded, hexagonal-head bushing, which in turn pushed against a spacer ring or bushing around the punch. This spacer ring pushed in turn on the bottom of the punch head, holding the punch head against the end of the hole in the punch holder.
The purpose of using both a threaded hex bushing and a spacer ring bushing to hold the punch was to allow the punch to move slightly, or "float", when pressure was applied. This kept the punch aligned with the die bore in spite of slight errors of alignment in the press itself. As the years have gone by and better techniques, machinery, jigs, and experience applied to making Corbin presses, it has become less and less important to provide so much "float" in the punch alignment system. The precision of the presses today is several orders of magnitude better than the original production. Thirty years of experience in building presses has brought about significant improvements in their alignment.
Today, the bushing system has outlived its original purpose. There is no need for more than a few thousandths of "float" to allow for possible self-alignment of the punch and die. By eliminating the bushing and making the head itself longer by the same amount, it is possible to hold the punch more precisely while honing, lapping, and doing other finish work on the "business" end of the punch. The ring was one more part to lose, even for experienced bullet makers. Beginners sometimes put the ring in the punch holder behind the punch head, which allowed the punch to smash the ring into the punch holder and damage both parts. And finally, a hardened steel ring adds unnecessary cost to the punch assembly (for .40 caliber and up, as the hex bushing and ring bushing were fastened to them with a removable punch head because the standard bushings that come with the punch holder would not slip over a punch that large).
BENEFITS:
- Less parts to assemble when changing punches.
- No chance of incorrect assembly or damage to holder.
- More precise holding during production provides higher accuracy.
- Fewer parts means holding the line on future prices.
- Less assembly work on large caliber punches means faster delivery.
Since there is no disadvantage to the user, and five advantages, it was not difficult to make the decision to change punch designs. The only disadvantages are in making the transition from old literature, books and publications which show the use of the spacer ring, to eventual new instructions and illustrations that do not show it, and in the possibility that someone who is used to the old design or reads the old published literature will be confused by the lack of a ring and longer head on the new punches. Informational notes will be sent with all new requests for information, all book packages and packaged sets of dies to correct the existing published instructions, until such time as the last of those publications are replaced. At that time a historical note about the earlier version, as compared to current version of the punch and punch holder assembly, will be included in the books, for those who acquire used equipment of the old style and need to understand the purpose of the ring spacer.
The new punch design is used WITHOUT a spacer ring. That is the ONLY difference in its use. It is fully interchangeable with the original punch in every other way, fits the same dies and presses and punch holders so long as the ring is not used.
Start writing here...
About Corbin Punch Types