One of the first questions a shooter may ask about swaging is whether a conventional, mass-produced reloading press can be used.
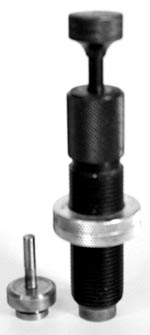
The answer depends on what specific bullet caliber and style you want to make, how fast and easily you wish to make it, and whether you plan to expand to other calibers or just make only one specific caliber. A conventional reloading press CAN be used to make these bullets:
If you want to make jacketed rifle bullets in calibers larger than .243, or rebated boattail bullets, or any bullet with the ogive made tangent or jointed at a secant angle to the shank (no step), then it is best to use a swaging press and the kind of dies which are made for it. The alignment, power, and precision of a swaging press, used with the special dies made for it, open unlimited possibilities compared to a reloading press and the dies which must be fitted to it. If you plan to make ANY bullet in commercial quantity, for resale in a small home business (or for yourself) at levels of more than about a thousand bullets a month, it simply does not pay to use a reloading press. Swaging presses are so much faster (over 300%) that you would waste far too much time with each bullet, in a reloading press kind of die. |
Are Dies Interchangeable Between Presses? You can use any die ending in "-R" in a reloading press, so long as the reloading press has a 7/8-14 thread single station head (not a turret style) and a standard T-slot ram using "RCBS" style shell holders. The -R dies (which have a -R following the catalog number) come with an external punch fitted to a base that looks like a shell holder. The -R type dies will also work in any Corbin swage press. But they work exactly like they would in a reloading press, and cannot take advantage of the built-in ejection, because that only works if the die and internal punch fit into the ram. Jacket and bullet reducing dies, on the other hand, work the same way in either press. You just have more leverage with the swage press. The -S or -H type dies (for Corbin swage presses only) do NOT work in a reloading press. There is no way to install them in the ram. The reloading press has no method of ejection, of holding the internal punch, or of holding the ram-mounted die. |
What's Wrong with a Reloading Press?
Nothing, if you use it for reloading. But for use as a bullet swaging tool, here are some of the reasons you'd find an actual swage press, designed from the ground up for swaging, to be far easier, faster, and more enjoyable:
A reloading press is "upside down" for swaging.
In a reloading press, the die must screw into the press head. The external punch, which pushes the components into the die, must snap into the T-slotted ram. You must pick up the component, push it upward into the bottom of the die, and hold it with your finger while you carefully raise the ram and punch, and slide the punch past your finger (don't pinch your finger in the process!).
Then, you apply gentle pressure to swage the bullet, and lower the ram. But there is NO ejection system for swaging built into a reloading press! To get the bullet back out of the die, you must pick up a mallet and tap on a plunger or K.O. rod placed in the top of the swage die. Meanwhile, your other hand must catch the bullet as it flys out of the die. If you don't catch the bullet, it will bounce off the press and fall to the floor.In contrast, a swage press is made so the die goes in the ram
This means you simply DROP the component into the upward facing die mouth. Gravity is on YOUR side with the swage press.
Then, you raise the ram, engaging the external punch automatically, as it is held in a floating punch holder in the press head. Adjustment of weight and pressure is done by turning this punch holder up or down in the press head. So far, you could have used one hand for all of this.
The bullet is now swaged with gentle pressure, but using less than half the effort because the swage press has about 235% more leverage than a reloading press. (The swage press has a 180-degree toggle travel as compared to the typical 135-degree limit on most reloading presses, and half the stroke length of a reloading press when in the short-stroke setting. Leverage is the ratio of ram movement divided into the distance your hand travels, in an arc, to achieve the ram movement.)
Now, you lower the ram and the bullet is automatically pushed out of the die, resting at the die mouth for you to pick up. Ejection is built into the press. You do NOT have to buy the additional parts built into every single reloading press die, since you pay for them just one time when you buy the swage press. This makes the press much faster to use, but also reduces the price of each die compared to a reloading press swage die.
Most reloading presses are built for mass marketing
There's nothing wrong with that: they serve their purpose of meeting the minimum requirement for reloading at a good price. But they are sold through jobbers, distributors, and dealers in most cases. That means, rule of thumb for manufacturing, that the material and labor you get in each one has to be about 25% of the retail cost. The other 75% pays for distribution, marketing, transportation, advertising, promotions, inventory taxes, overhead of each of the three kinds of businesses responsible for getting it in your hands,and of course a fair margin for each of them so they have some incentive to do it!
On the other hand, if you pay $100 retail for a mass marketed press, you are buying what would essentially cost $25 at the factory door. If you are paying nearly $750 for a product that is sold directly from the factory door to you, bypassing the conventional distribution costs, it means you are getting a product which would be priced, in a retail store, at nearly $3000. There are good reasons for this. If it were simply profit, everyone else would be jumping to do the same thing.
What you are getting is a tremendous amount of precision hand work, bearings in every moving part (four sets of roller bearings just in the links alone!), hardened tool steel pivots and industrial chromed tool steel ram, hand fitted ram bearings to align and guide the ram straight on axis with the press head, dual stroke (or triple stroke in the Mega Mite) leverage system for both swaging and high precision reloading... in fact, even the nuts and bolts are chucked up in lathes and turned on the bottom sides so that the surface is perfectly perpindicular to the axis (hardly any nuts and bolts come that way).
Swage presses are optimized for swaging forces The swage press uses a steel head and support structure, with bearings in every moving part, and is aligned with precision alignment jigs as it is assembled. The head can be removed and replaced, in case you ever wish to experiment with unusual thread sizes of dies for reloading (yes, the swage press is a reloading press also -- "on steroids" as they say). A reloading press is generally made from a casting, with a hole drilled for the ram, and another hole drilled and tapped for the head. You cannot "adjust" the alignment. If there is angular misalignment, or co-axial misalignment of the head and ram, nothing can be done about it. And for reloading, it probably does not matter very much except to benchrest shooters. There is enough "tolerance" in the loose fit of shell holders and cartridge cases in the shell holders so that some alignment error can be tolerated. The swaging press can be aligned in the field, with alignment test jigs available from Corbin. It is not necessary unless you were sky diving with your press and it forgot to open its 'chute. But it can be done. Therefore, if you should ever have the need to realign the axis of the head and ram, the swage press allows it. Reloading presses are usually made from one raw iron casting, typical tensile strength of 35,000 to 40,000 psi. The steels used in the Corbin swage presses have typical tensile strengths of more than 125,000 psi. This means virtually nothing except that the swage press uses tougher materials. A swage press can be smaller, physically, and still be much stronger than a cast frame press. You will never need to apply more force than the press can handle, because if you do, you'll pop the swage die long before the press feels any pain! Reloading presses support the head with the same continual casting as the rest of the frame. Corbin swaging presses, such as the CSP-1 S-press, utilize compress/torsion steel support struts. These are composites of a compression force, applied to two lengths of hydraulic cylinder tubing cut to use as head supports, and a torsion force applied through a hardened washer and industrial grade nut (with the bottom machined in a lathe for perfect 90-degree angle to its axis before assembly) to long threaded rods passing through the middle of the cylinders. This is illustrated on the CSP-1 page. But the point is, you are getting a system of alignment and support that is engineered to stay aligned, and can be adjusted in several ways if for any reason it suffers a physical trauma (sky diving?). How do you "fix" the reloading press to be dead-on axis, other than completely reboring, lining, and line-honing it and then fitting a new ram (which would cost about as much as a proper swage press)? |
Bottom Line: If you only want to make one caliber, maybe two, and the limitations of a reloading press are not bothersome to you, then a swaging outfit that works in a reloading press will be fine. If you plan on expanding to other calibers, need long range rifle precision or benchrest quality, want to make more interesting styles of bullets such as the RBT bases, plan on making very many bullets at a time, or just want to work with the best tool for the job, then a swaging press and the special dies that work only in a swaging press are more suitable. Corbin Swage Presses |
Swaging Press or Reloading Press?