The tools you need depend on the bullet you want to make:
- A lead bullet with a step or shoulder between nose and shank (like a Keith or SWC or Wadcutter) can be made in a single die, called the "LSWC-1". Hollow base shotgun slugs, and airgun pellets, are also made with this kind of die.
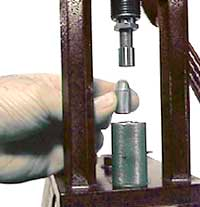
- Calibers from .10 to .458 inch can use the LSWC-1-S die and the CSP-1 S-Press.
- Calibers from .459 to 1.00 inch can use the LSWC-1-H die and either the CSP-2 Mega Mite or the CHP-1 Hydro Press.
- A reloading press can also be used, with the PRO-1-R ProSwage die.
- Calibers from .10 to .458 inch can use the LSWC-1-S die and the CSP-1 S-Press.
- A lead bullet without a step or shoulder between nose and shank (a smooth ogive bullet) can be made in a two dies, called the core swage (CSW-1) and the point form (PF-1).
- Calibers from .10 to .458 inch can use type-S dies and the CSP-1 S-Press.
- Calibers from .459 to 1.00 inch can use type-H dies and either the CSP-2 Mega Mite or the CHP-1 Hydro Press.
- A reloading press can also be used with a custom CSW-1-R and custom PF-1-R die. Except in .224, .243, and certain pistol calibers (.32 to .38), the -R dies are only available on custom order.
- Calibers from .10 to .458 inch can use type-S dies and the CSP-1 S-Press.
- A jacketed bullet with a step or shoulder between nose and shank can be made in a two dies, called the core swage (CSW-1) and the core seater (CS-1). This combination is called the "JSWC-2-S" or "JSWC-2-H". You can order the two individual dies, or the single catalog number for them both.
- Calibers from .10 to .458 inch can use type-S dies and the CSP-1 S-Press.
- Calibers from .459 to 1.00 inch can use type-H dies and either the CSP-2 Mega Mite or the CHP-1 Hydro Press.
- A reloading press can also be used with a custom CSW-1-R and custom CS-1-R die. Except in .224, .243, and certain pistol calibers (.32 to .38), the -R dies are only available on custom order.
- Calibers from .10 to .458 inch can use type-S dies and the CSP-1 S-Press.
- A jacketed bullet without a step or shoulder between nose and shank, and a flat or cupped base can be made in a three dies: the core swage (CSW-1), the core seater (CS-1), and the point former (PF-1). This combination is called the "FJFB-3-S" or "FJFB-3-H". You can order the three individual dies, or the single catalog number for all three in a matched set. The core swage (CSW-1) is optional, but is usually desired as part of the set, for more accurate weight control.
- Calibers from .10 to .458 inch can use type-S dies and the CSP-1 S-Press.
- Calibers from .459 to 1.00 inch can use type-H dies and either the CSP-2 Mega Mite, or the CHP-1 Hydro Press.
- A reloading press can also be used for .224 or .243 bullets, with the BSD-224R or BSD-243R die sets, which have the CS-1-R and PF-1-R (the CSW-1-R can be ordered as an option).
- Calibers from .10 to .458 inch can use type-S dies and the CSP-1 S-Press.
For a good background in swaging, get Handbook of Bullet Swaging, No.9 on CD-ROM. This gives you quick lookup and instant access to information on nearly every aspect of swaging at very low cost. Corbin bullet design software can help you design bullets without a math or engineering background: just fill in the blanks, click "calculate", and get a wealth of information about any bullet your imagination can suggest! |
Dies are classified by the kind of press they fit, and the kind of operation they perform.![]()
|
Making A Bullet The first step in swaging any bullet is adjusting the weight of the core. The core can be lead, or some other material. It can also be the entire bullet (for lead bullets), or just the filling for the jacket (which is the cup or shell around the core). This is an optional but highly recommended first step. You can skip it and make sure your cut or cast cores are as accurate in weight as possible by careful preparation. In that case you do not need the core swage (CSW) die. The bullet can be made in one step if it has no jacket, and can have a shoulder between the shank and nose. It can be made in two steps, in a core swage and a core seat die, if it has a jacket that does not go past the shoulder. If it has a flat, cup, dish, or hollow base, it can be made in three dies, without a shoulder, with or without a jacket. The jacket can be put in backward to make a full metal jacket, or the lead core can be shorter than the jacket for an open tip. Rebated boattail bases and lead tips are created with other steps. No more than five basic operations are required for swaging any of the bullet styles. Each step is a single stroke of the press. Each stroke takes from 2 to 5 seconds, depending on the press and the particular operation. Simple lead bullets can be made at 10-12 per minute, jacketed semi-wadcutters at 5-6 per minute, full jackets, soft or hollow point flat bases at 3-4 per minute, and rebated boattail open tips at 2-3 per minute. The important thing to keep in mind about swaging is that the process works by putting very high pressure on the filling or core, which compresses in length and expands in diameter, pushing the jacket (if used) into exact conformity with the inside of the die. The component you are swaging expands in diameter. When you release the pressure to eject the bullet, the materials shrink back very slightly to release from the die. The jacket stretches, and every void within the sealed die is filled with material. Whatever pressure is applied to the core, or base of the bullet, is also applied to every other part. | ||||||||||||
To get a better understanding of swaging, click the subjects in the following table. (Core swaging is the first operation in making nearly any bullet...)
|
Get Started Swaging With Corbin